In today's competitive and quality-focused manufacturing landscape, ensuring product consistency and compliance is more important than ever. Whether it's pharmaceuticals, biologics, or advanced therapies, companies must meet strict quality standards and regulatory expectations throughout the production cycle. One of the most essential tools in achieving these goals is In-Process Testing (IPT).
In-process testing plays a vital role in real-time quality control, allowing manufacturers to monitor, evaluate, and optimize their production processes at every stage. This proactive approach reduces waste, enhances efficiency, and most importantly, ensures that the final product meets defined quality and safety standards.
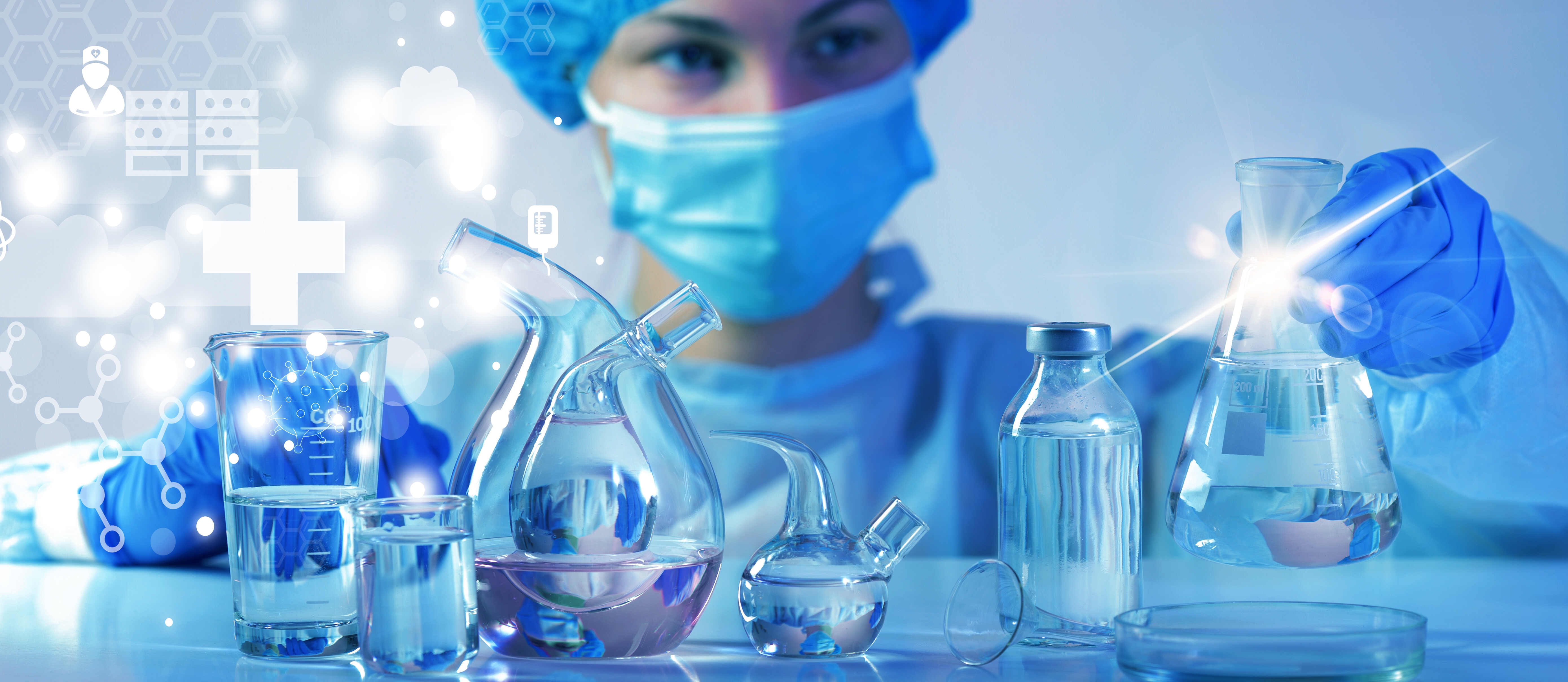
What Is In-Process Testing?
In-process testing refers to the examination and evaluation of intermediate materials and components during various stages of production. Unlike end-product testing, which only assesses the final product, IPT helps detect issues early in the process, allowing for immediate corrective actions before further value is added.
In regulated industries like pharmaceuticals, biotechnology, and medical devices, in-process testing is not just a best practice—it’s a requirement. Regulatory bodies such as the FDA, EMA, and WHO mandate strict adherence to Good Manufacturing Practices (GMP), which emphasize quality assurance at every phase of production.
Key Benefits of In-Process Testing
Maintains Consistent Quality
IPT ensures that each unit of product manufactured meets predefined quality criteria.
Regulatory Compliance
IPT demonstrates control over the manufacturing process, which is a critical requirement for regulatory approvals and inspections.
Operational Efficiency
Real-time feedback from in-process tests allows for process adjustments on the fly, reducing downtime and improving yield.
Supports Quality by Design (QbD)
In-process controls are a core component of the QbD approach, which aims to build quality into the process rather than relying solely on end-product testing.
Common In-Process Tests in Biopharmaceutical Manufacturing
In the biopharmaceutical and advanced therapy industries, in-process testing is used extensively to control and verify critical quality attributes (CQAs) and process parameters. Common tests include:
pH Monitoring – Ensures optimal conditions for chemical reactions and cell culture viability.
Osmolality – Crucial in maintaining proper cell function during bioprocessing.
Cell Viability and Count – Monitors the health and proliferation of cells in cell therapy and biologics manufacturing.
Protein Concentration and Purity – Ensures the desired product is present at the correct levels.
Sterility Checks – Detects microbial contamination to maintain aseptic conditions.
Identity and Potency Tests – Confirms that the intermediate product retains its intended biological activity.
In-Process Testing in Cell and Gene Therapy
In Cell and Gene Therapy (CGT) manufacturing, where each batch can be patient-specific, in-process testing takes on an even greater role. These therapies involve highly sensitive biological materials and complex workflows, with little room for error. IPT ensures that cells are healthy, properly modified, and free from contamination at each critical step, from collection and expansion to purification and formulation.
Some CGT-specific in-process tests include:
Transduction efficiency
Vector copy number
Cell identity and phenotype
Contamination and sterility
Cryopreservation viability
Effective in-process testing helps meet regulatory expectations and ensures that life-saving therapies reach patients safely and efficiently.
Integration with PAT and Automation
As technology evolves, Process Analytical Technology (PAT) and automation are becoming more common in supporting IPT. These systems enable real-time data collection, predictive analytics, and continuous monitoring—enhancing decision-making and reducing manual intervention.
Integrating IPT with digital platforms offers several advantages:
Improved accuracy and repeatability
Faster response to deviations
Reduced human error
Seamless data tracking and reporting
By combining IPT with modern tools, companies can achieve greater process control and scalability.
Regulatory Importance
Regulatory agencies around the world emphasize in-process controls as a foundational element of GMP. The FDA, for example, requires detailed documentation of in-process testing procedures and results to ensure that products are manufactured under controlled conditions.
ICH guidelines (such as Q8, Q9, and Q10) further support the integration of risk management and quality systems with in-process testing to create a robust, science-based manufacturing framework.
Conclusion
In-process testing is not just a regulatory requirement—it's a smart, proactive strategy that ensures product quality, enhances operational efficiency, and builds confidence in your manufacturing process. By embedding quality at every step, manufacturers can avoid last-minute surprises, reduce costs, and deliver consistent, high-quality products to the market.
As industries like biologics, cell and gene therapy, and personalized medicine continue to evolve, in-process testing will play an even more vital role in meeting the demand for precision, safety, and speed. Investing in robust in-process testing today lays the foundation for a compliant, agile, and future-ready manufacturing operation.