Inspections can either make or break a construction schedule. Whether you're a homeowner tackling a remodel or a contractor on a commercial site, being ready for your inspection isn’t just about checking boxes, it’s about having your project ready to thrive.
A failed inspection can result in costly delays, rework, and even permit loss. Yet with proper planning, you can turn this much-dreaded milestone into a smooth, predictable step in your construction journey.
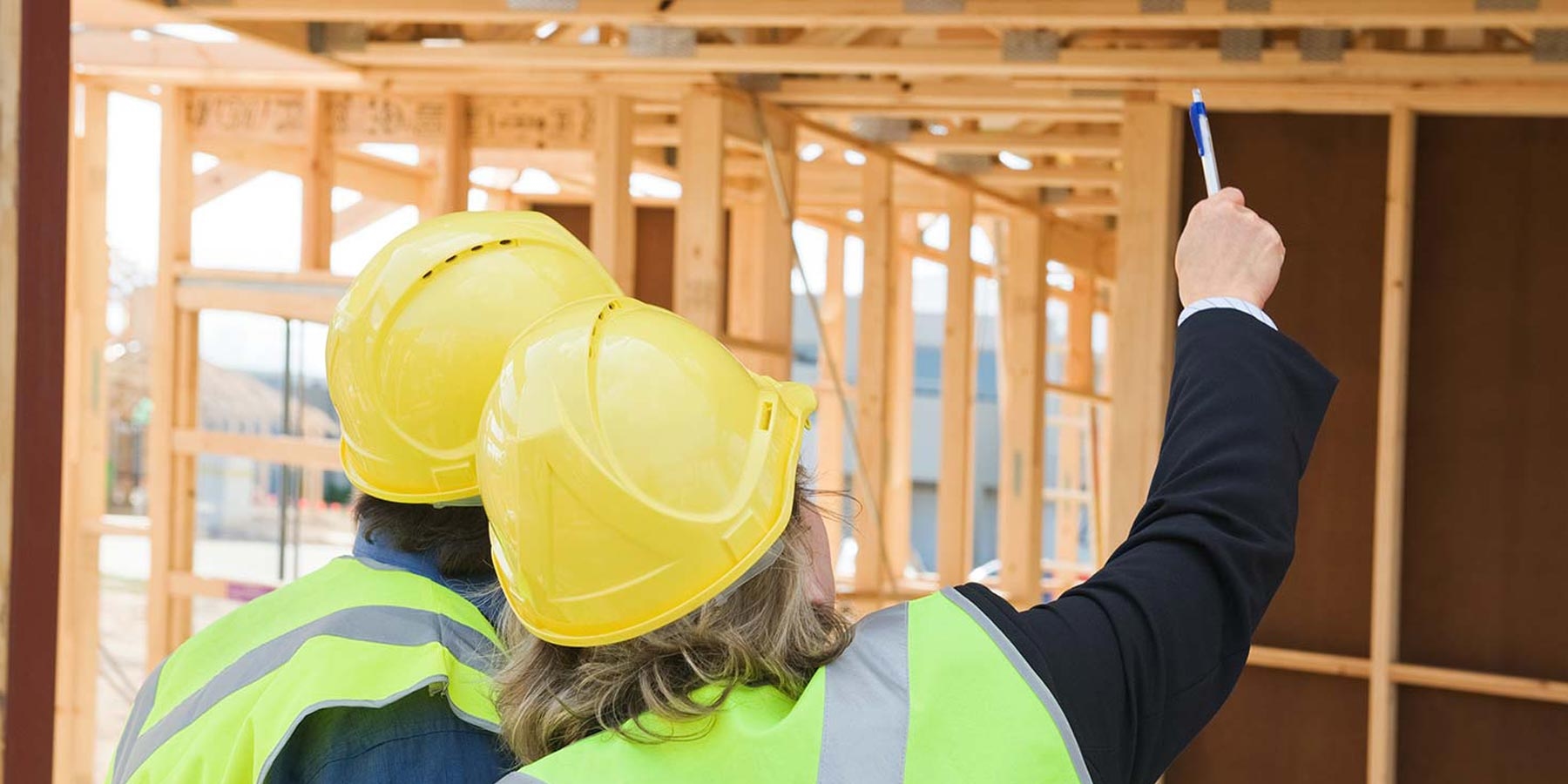
Let’s walk through the process of planning for and passing your next building inspection.
Why Most Building Inspections Fail
Overlooked Code Requirements
One of the most common causes of inspection failures in the U.S. is non-compliance with local building codes. These codes vary significantly between states, counties, and cities. Relying on outdated or generalized standards is a sure path to failure.
Sites Not Ready or Incomplete Work
Some contractors schedule inspections prematurely. Incomplete drywall, loose electrical wiring, or missing fireblocking can all result in automatic delays.
Poor Communication with Inspectors
Inspectors are often seen as obstacles, but in truth, they’re allies in ensuring safety and compliance. Miscommunication, incomplete documentation, or an absent site manager during inspection day can result in unnecessary tension and setbacks.
Step-by-Step Guide to Prepare for an Ideal Building Inspection
Step 1: Know What Kind of Inspection You're Performing
There’s no one-size-fits-all inspection. You may be preparing for one of the following:
Foundation Inspection
Framing Inspection
Rough-in (Electrical, Plumbing, HVAC)
Insulation Inspection
Final Inspection
Carefully review which inspection is coming up and what’s required. Your local building department will likely provide checklists; use them to your advantage.
Step 2: Ensure Compliance with Local Codes
U.S. building codes stem from the International Building Code (IBC) and the International Residential Code (IRC) but are adopted and enforced locally.
Reference your city’s amendments and the Authority Having Jurisdiction (AHJ).
Make sure your plans and drawings are updated with 2025 code requirements.
Pay attention to energy codes, fire safety, egress, and accessibility standards.
Pro Tip: When outsourcing construction takeoff services, ensure they include local code compliance and material specs in their scope.
Step 3: Do All Work Before Scheduling Inspection
Inspectors expect total readiness. Make sure:
Electrical wiring is tied and capped
Plumbing systems are pressure-tested
HVAC units are roughed-in or installed per stage
Wall sheathing is installed with no firewall breaches
Work surfaces are clean and free of debris
Don’t rush into scheduling. Too many failed inspections can trigger red flags or even penalties.
Step 4: Have All Documentation Ready
Ensure these documents are available and accessible on-site:
Approved building plans
Original permits and change orders
Letters from engineers or architects (if applicable)
Logs of prior inspections
Manufacturer training manuals for installed systems
An organized project shows professionalism and readiness.
Step 5: Make the Site Safe and Accessible
Your inspector must safely access all areas. Make sure to:
Clear pathways to crawlspaces, attics, and utility rooms
Provide sturdy ladders for roof or ceiling access
Illuminate dark spaces like basements or mechanical rooms
Power down dangerous equipment during inspection
Security Tip: If no workers are present, ensure someone is on-site or available to guide the inspector and provide access.
Typical Issues That Result in Re-Inspections
Poorly Connected Structures
Loose joist hangers, missing anchors, or uninstalled hurricane clips are common structural oversights.
Insufficient Fire Blocking or Draft Stopping
Framing inspections often fail due to skipped firestops or draft-stopping in multi-floor walls or penetrations.
Defective Electrical or Plumbing Rough-Ins
Common issues include:
Wires in metal boxes without grommets
Missing nail guards
Unsupported or unstrapped plumbing pipes
Lack of pressure testing
Bonus: Why Construction Takeoff Services Leave You Inspection-Ready
Accurate material measurement is key to pre-inspection success. This is where construction takeoff services play a critical role. They help you:
Forecast material requirements to avoid shortages
Align project scope with building codes and specifications
Stay on budget and on schedule
Ensure insulation and systems are accounted for before audits or energy code reviews
Having a professional estimating or takeoff team helps eliminate last-minute surprises when the inspector shows up.
Final Remarks
Building inspections shouldn’t be intimidating. With proper planning, attention to detail, and thorough documentation, you can turn inspections into a predictable, even beneficial, checkpoint.
Build strong relationships with your inspectors.
Follow local codes to the letter.
Maintain a clean, safe, and transparent job site.
Use services like construction takeoff to keep materials and timelines on track.
Frequently Asked Questions
Can I pass a building inspection if there’s one minor outstanding issue?
No. Even one overlooked safety or code item can result in a failed inspection.
How soon can I request a re-inspection if I fail?
That depends on your jurisdiction. Some areas allow next-day re-inspections, while others impose delays or fees.
Do I have to be present for the inspection?
It’s highly recommended. Either you or someone familiar with the project should be present to answer questions and provide documentation.