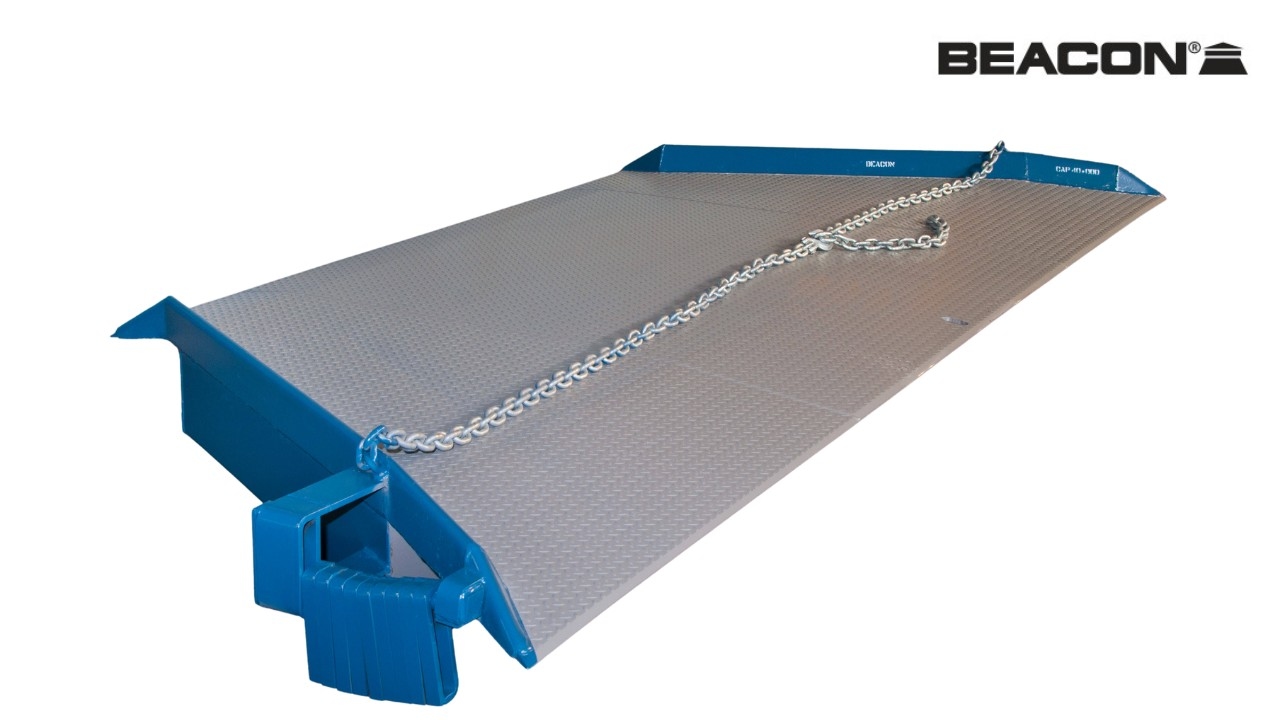
Rail dock boards are heavy-duty, portable steel platforms with raised side curbs and non-slip surfaces, designed to bridge the gap and height difference between a loading dock and a railcar. They provide a stable, secure path for forklifts, pallet jacks, or workers to move freight safely and efficiently during railcar loading and unloading. Built to handle heavy loads and absorb impact, these boards help maintain smooth, uninterrupted workflow in demanding industrial settings.
To ensure a safe and proper fit, rail dock boards are often custom-engineered based on the dock layout and railcar type. Specifications such as bend angles, width, length, and weight capacity are tailored to match the exact needs of the facility. This level of precision supports compatibility with a wide range of railcars, including refrigerated units and boxcars used in manufacturing, paper, and lumber operations.
Choosing the right rail dock board is essential for maintaining safety, minimizing load times, and ensuring consistent productivity in any rail-based operation.
Common Rail Dock Board Designs
Rail dock boards are available in several designs, depending on your layout and loading needs:
Rectangular Boards work well when your forklift can approach straight on.
Flared Boards are ideal for tight turns or angled entry into the railcar.
Specialty Boards are designed for specific railcars, such as plug doors or refrigerated units, and even for transferring goods between two railcars.
Most boards feature a steel tread surface with a non-slip texture, which helps maintain traction in dusty or wet industrial environments.
Steel vs. Aluminum: What to Choose
Steel is the most common material for rail dock boards. It is strong, durable, and capable of handling up to 90,000 pounds or more. This makes it ideal for heavy forklift use and continuous operations.
Aluminum boards are lighter and naturally resistant to corrosion, but they generally support lower weight limits, usually under 15,000 pounds. They are easier to move and better suited for light-duty work or environments where rust is a concern.
Tip: Use steel if you need maximum durability. Choose aluminum if weight and corrosion resistance are more important than capacity.
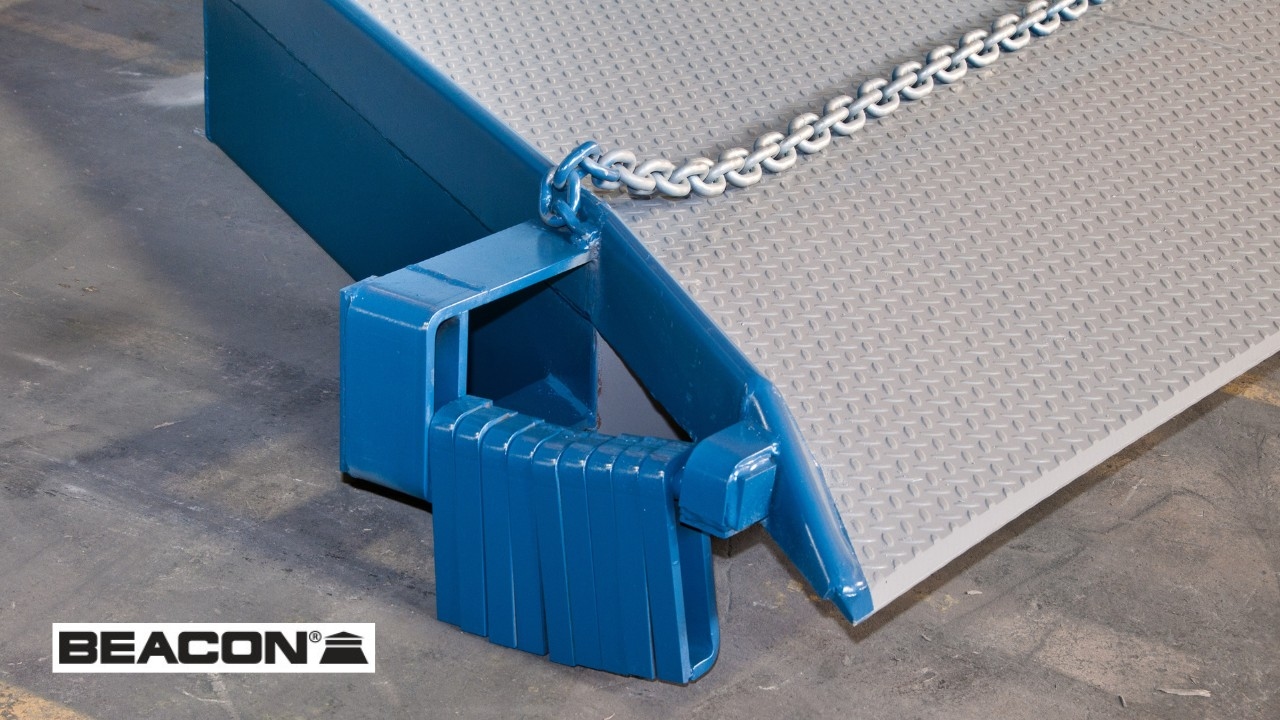
Weight Capacity and Sizing Guidelines
To ensure safety, always choose a dock board that supports your equipment, cargo, and a safety margin:
Capacity Rule of Thumb:
3× forklift lifting capacity for four-wheeled forklifts.
4× for three-wheeled forklifts.
Example: A 5,000 lb forklift? Choose a board rated:
15,000 lbs (4-wheel)
20,000 lbs (3-wheel)
Dimensions Matter
Width: At least 12" wider than the equipment’s wheelbase for safe maneuvering.
Length: Must span the height difference between the dock and the railcar while maintaining a safe incline.
~10–14% grade for electric/manual equipment.
~19% grade acceptable for gas/diesel forklifts.
Also, account for the horizontal gap; railcars don’t always sit flush to the dock. Ensure the board is long enough to reach the car securely.

How to Select the Right Rail Dock Board
Choosing the correct rail dock board involves more than picking one off the shelf. It requires a clear understanding of your facility’s operational demands, safety requirements, and layout constraints. Here’s how to make an informed decision:
1. Understand Load Requirements
Start with your forklift’s specifications and cargo weight. Calculate the combined weight of the forklift, operator, and the heaviest load it will carry. Use this number to determine the minimum capacity rating for your dock board.
For four-wheel forklifts, multiply the lifting capacity by 3
For three-wheel forklifts, multiply by 4
This built-in safety margin accounts for momentum, braking, and uneven load distribution. Going slightly above the minimum capacity can extend the board’s service life, especially in high-traffic or 24/7 operations.
2. Measure Carefully
Accurate measurements are essential for selecting the right board dimensions. Measure the following:
Dock height
Railcar floor height (both typical and maximum)
Horizontal gap between the dock face and the railcar
Railcar door width
These dimensions help determine the proper length (for a safe slope) and width (for forklift clearance) of the dock board. A board that’s too short or narrow can compromise safety.
3. Evaluate Space Constraints
Examine the layout around your loading area. Determine if forklifts have a straight path into the railcar or must approach at an angle.
Use rectangular boards for straight-on access
Use flared-end boards for angled approaches or tight spaces
Also consider:
Dock obstructions like bumpers or levelers
Overhead or side clearances
Turning radius requirements
These details will guide the right board shape and features.
4. Consider Portability
Decide how often the board needs to be moved or repositioned. If it won’t stay in one place, prioritize portability features:
Forklift-compatible lift loops or chains
Manageable weight for your equipment
Aluminum material (lighter, ideal for occasional use)
Steel boards are heavier but more durable for permanent or high-use setups.
5. Factor in Frequency of Use
High-frequency use places more stress on the board. If your board will be in service daily or across multiple shifts, invest in:
A higher-capacity model with stronger welds and reinforced structure
A backup board for maintenance or emergency use
Durability matters when the dock is a high-traffic point in your operation.
6. Account for Environmental Conditions
The operating environment has a direct impact on which rail dock board is best suited for your facility. Consider the following when selecting materials and surface features:
Aluminum is ideal for rust-prone areas or environments involving food, chemicals, or frequent washdowns, thanks to its corrosion resistance and non-sparking properties.
Painted or coated steel is recommended for outdoor use, offering high strength with added protection against weather and moisture.
Non-slip surfaces and high-visibility markings are essential when foot traffic is involved, helping prevent slips and improving operator awareness.
Choosing the right combination of material and finish ensures your dock board performs safely and reliably in any condition.
7. Consult with a Manufacturer or Distributor
Many manufacturers and distributors offer support to help you find the right dock board. Take advantage of:
Site surveys and measurement services
Custom-fit boards based on your equipment and railcar specs
Expert guidance on capacity, materials, and safety features
Avoid guesswork by working with an experienced manufacturer who can recommend or design a board tailored to your facility.
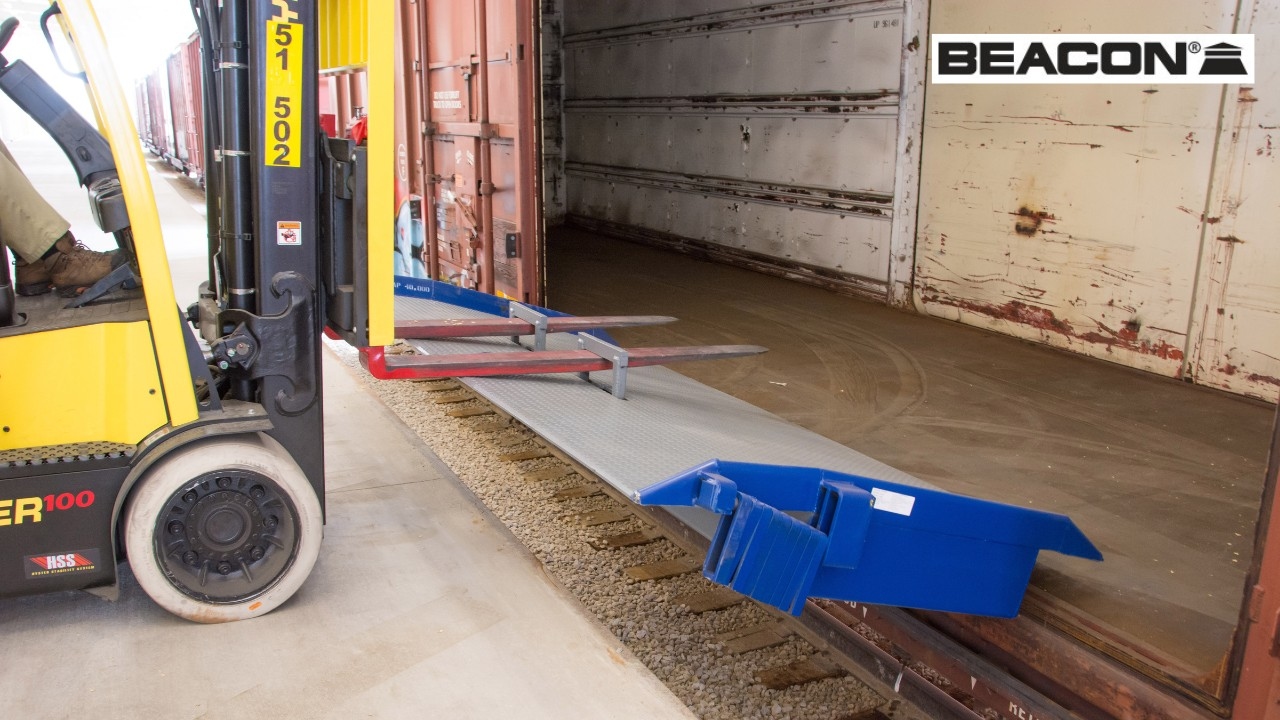
Where Rail Dock Boards Are Used
You’ll find rail dock boards in a wide range of settings:
Warehouses and Distribution Centers for moving palletized goods like lumber, metals, or paper rolls
Manufacturing Facilities where raw materials or finished products are loaded into railcars
Bulk Material Sites that handle super sacks, drums, or crates
Rail Yards and Intermodal Terminals, where car-to-car transfers may take place
In all these cases, a properly selected rail dock board is essential to connect your operations to the cost efficiency of rail transport.
Safety Features That Matter
High-quality rail dock boards include several built-in safety features:
Locking Rings or Pins to keep the board in place during loading
Lift Loops or Chains to allow easy forklift positioning
Raised Steel Curbs to guide wheels and prevent drive-off accidents
Non-Slip Surfaces for traction in slippery conditions
High-visibility markings to assist forklift operators during alignment
These features ensure the board stays put and reduces the risk of injury or damage.
Why the Right Rail Dock Board Matters
A rail dock board does more than connect your dock to a railcar; it plays a critical role in maintaining safety, minimizing downtime, and ensuring efficient material handling. The right board helps reduce equipment strain, improve loading speed, and create a safer, more reliable operation.
By carefully evaluating your load capacities, facility layout, and usage frequency, you can select a board that fits seamlessly into your workflow. Whether you're moving bulk freight, heavy machinery, or palletized goods, choosing the right board is a long-term investment in both safety and operational performance.
If you're unsure where to start, manufacturers and suppliers can offer expert recommendations or custom solutions designed around your specific railcar setup and workload.