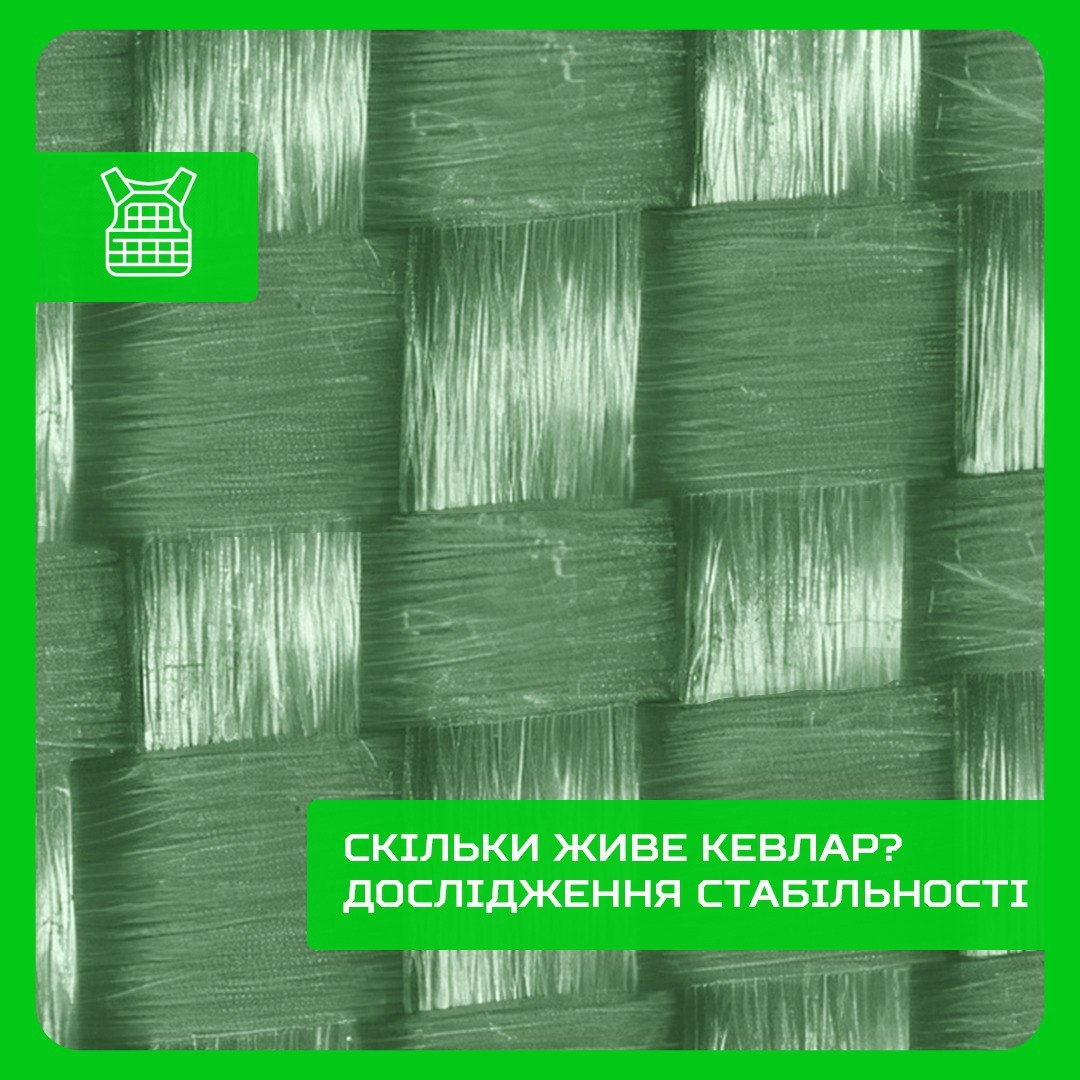
Дисклеймер: використано опубліковані у відкритих джерелах експериментальні дані, отримані сертифікованими науковими інституціями та співробітниками. Всі джерела вказано у кінці матеріалу. Якісні висновки носять рекомендаційний характер, бажано переглянути наведений матеріал повністю.
Чому Кевлар деградує?
Під торговою маркою Kevlar продаються матеріали, які є текстильними волокнами полімерних амідів, тобто жорстких пластмас, залитих епоксидною смолою або запаяних між пластинами іншого пластику.
Пластмаси, як загалом хімічно інертні матеріали, можуть втрачати свої властивості через такі чинники: опромінення ультрафіолетом, термічний розклад, течію (так, деякі тверді пластмаси можуть дуже повільно текти), хімічні реакції з водою та киснем повітря.
Молекули кевлару – жорсткі ланцюги, міцно зв’язані між собою хімічно. Тому він стійкий до практично всіх впливів, крім окиснення при опроміненні та реакцій з водою.
Крім хімічних факторів, на міцність впливає також механічна “спрацьованість” матеріалу, тобто скільки броню били, гнули, стріляли.
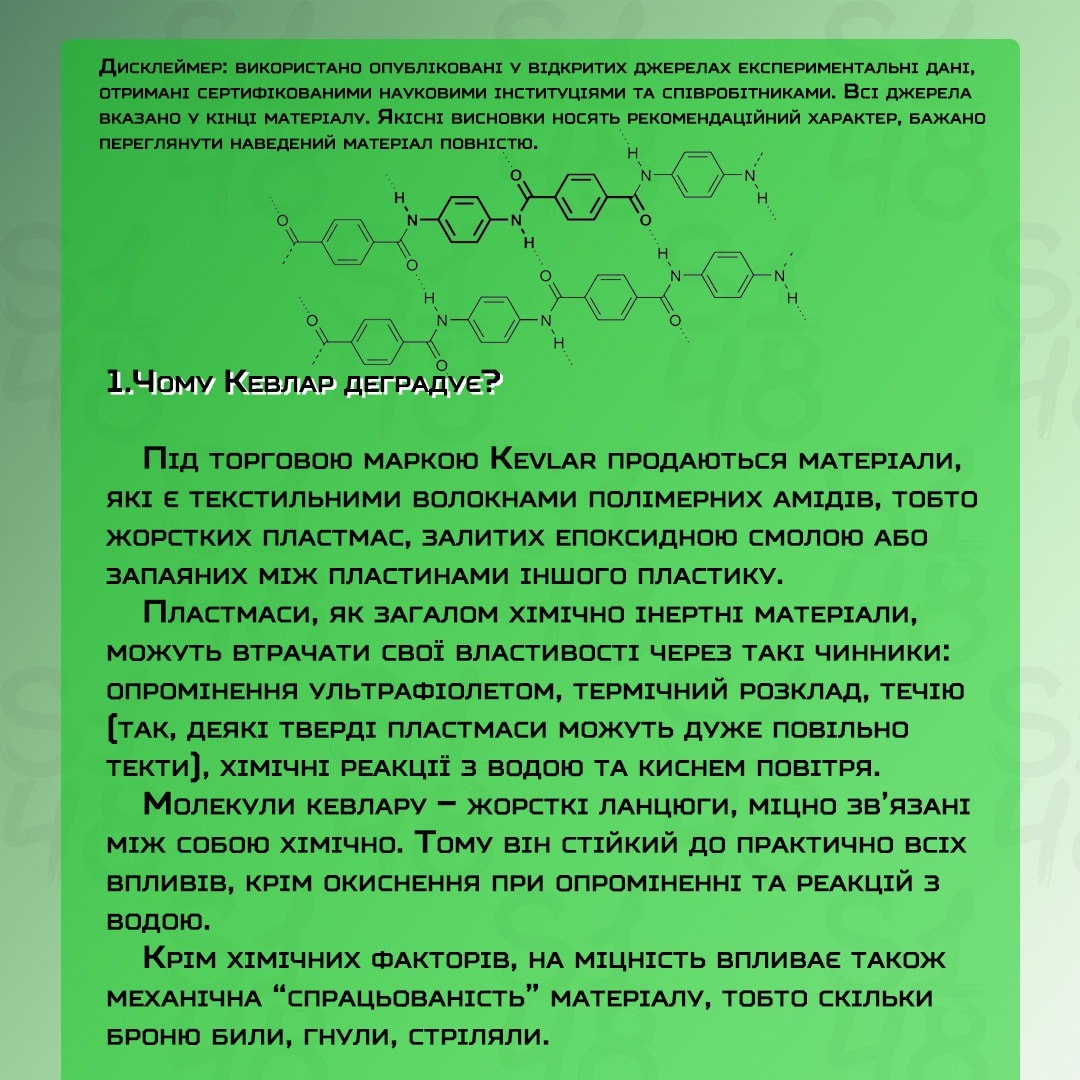
2. Як ми визначаємо що броня придатна?
Матеріали характеризуються безліччю механічних параметрів, але в цьому тексті будуть згадані лише границя міцності (максимальна сила розтягу, яка досягається за момент до розриву матеріалу) та модуль пружності (говорить про те, наскільки великий спротив матеріалу деформації).
Захисні матеріали за стандартами США прийнято характеризувати величинами V50 та деформацією при попаданні.
V50 – швидкість, за якої куля певного калібру пробиває плиту у половині випадків: у зразок випускається 10 куль, швидкість кожної наступної трохи вища за попередню. Якщо п’ята чи шоста куля починає пробивати жилет, середню швидкість 10 куль визначають як V50.
Деформація – глибина прогину плити при попаданні, характеризує міру захисту від заброневої травми.
У наведених дослідженнях застосовували свинцеві кулі калібрів .38 та .22 Long rifle.
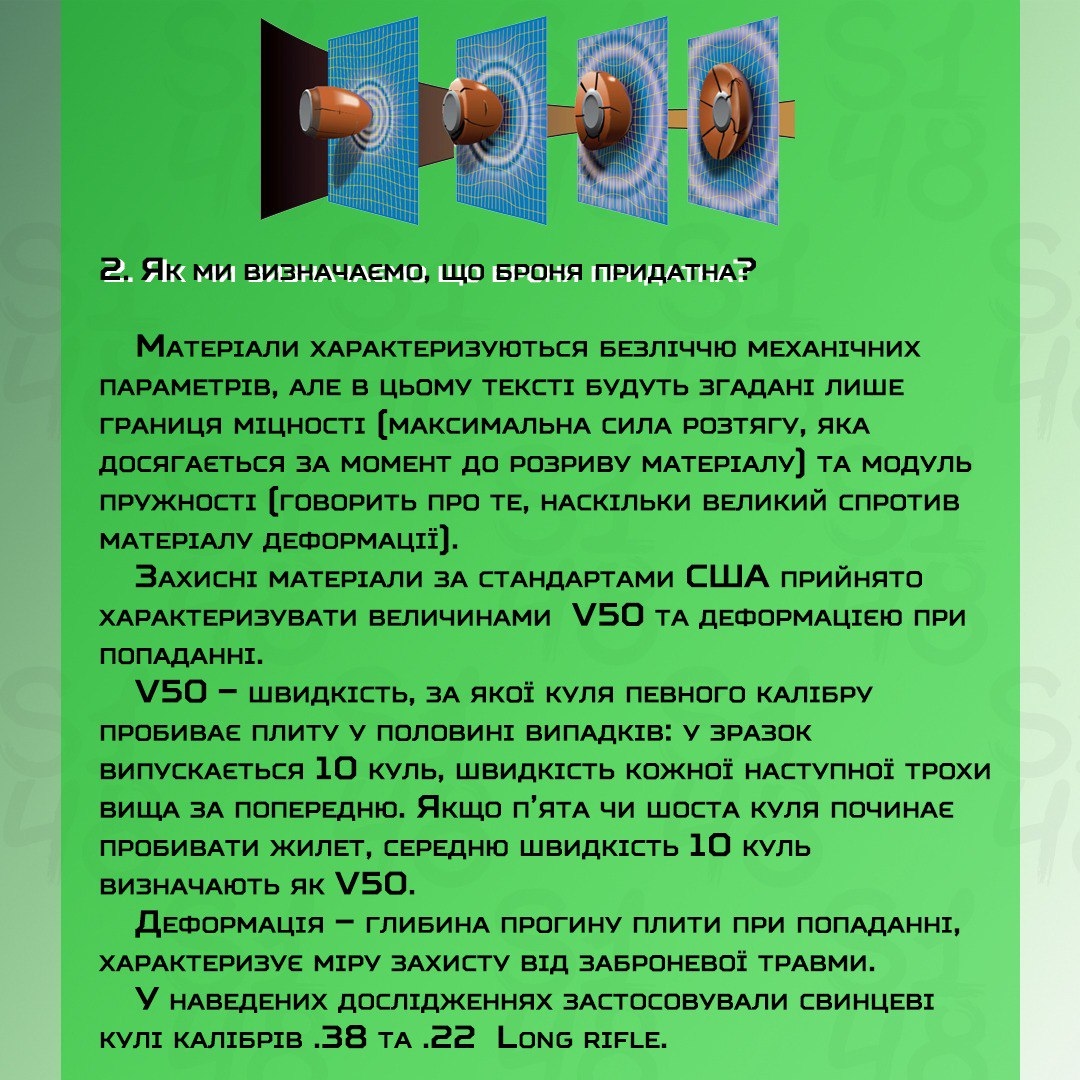
3. Звідки взялось 5 років?
Перші тести на стабільність кевлару провела компанія DuPont, винахідник та
виробник кевлару [1]. Вони здійснили дослідження механічних властивостей броні, вилученої в поліції після строку служби 3-5 років, та встановили, що оптимальний строк служби саме 5 років.
Але такий висновок викликав широку дискусію, бо насправді історія конкретних зразків була невідома: бралось як даність те, що жилети служили 50 робочих тижнів (5 робочих днів по 8 годин) на рік в умовах температури 36 градусів та 100-відсоткової вологості. Так і отримали приблизно 441 робочий день, тобто 5 робочих років.
Опоненти відзначали, що механічні властивості більше корелюють із візуальною поношеністю зразка, а не з віком.
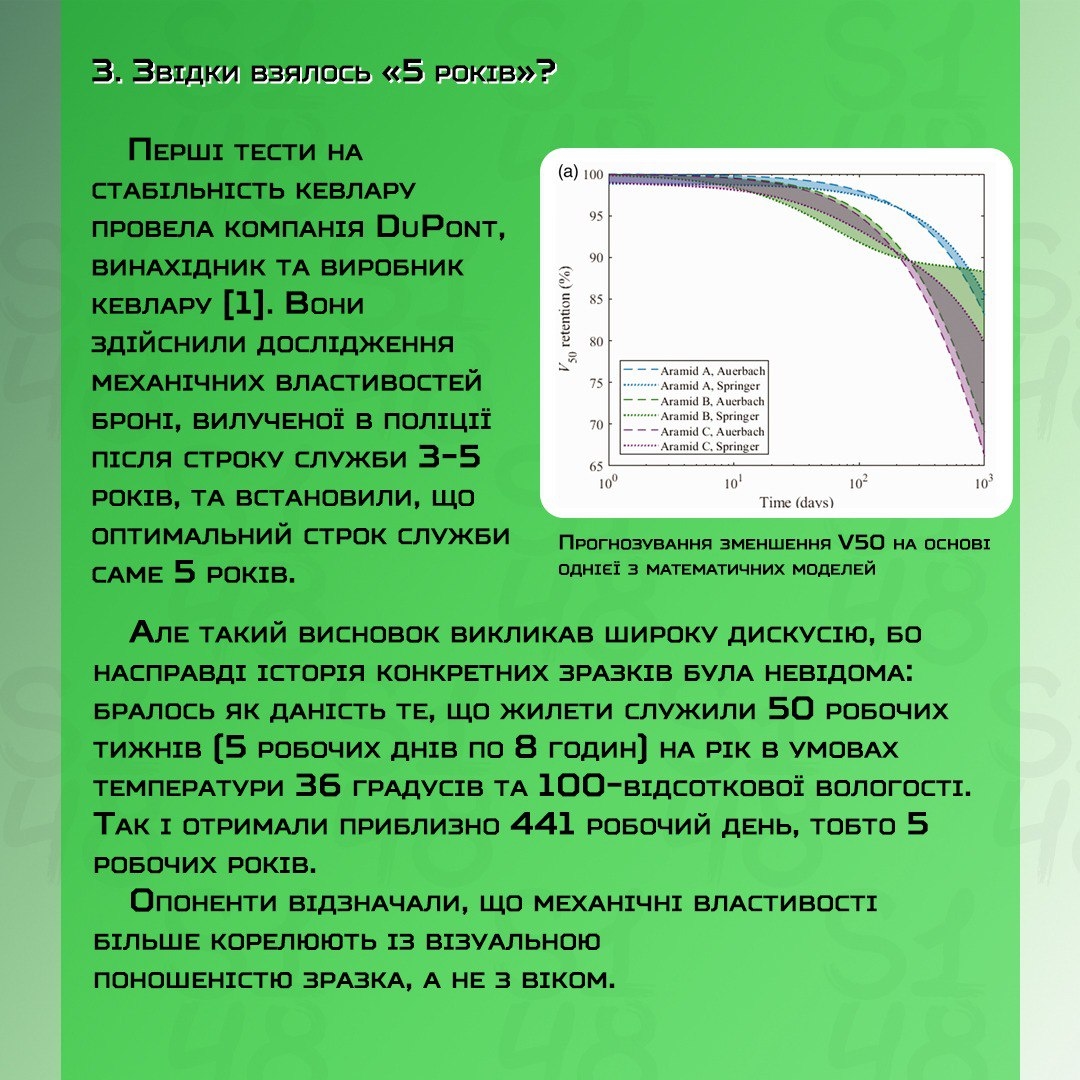
4. Натурні досліди
Наступним після виробника за справу взялося Національне Бюро Стандартів США [2]. Було взято 24 бронежилети, які прослужили 10 років із часу видачі. Також було детально (наскільки можливо) вивчено історію служби бронежилетів. Були як ті, що просто 10 років лежали на складі, так і ті, що активно використовували.
У результаті дослідження НЕ БУЛО ВИЯВЛЕНО ЧІТКОЇ ЗАЛЕЖНОСТІ МІЖ ЗНОШЕНІСТЮ ТА МІЦНІСТЮ. Різниця між новими та поношеними жилетами була приблизно така ж як випадкова різниця між новими жилетами з різних партій (за результатами тестів якості армією США), тобто приблизно 5 відсотків V50. Всі зразки відповідали стандартам якості.
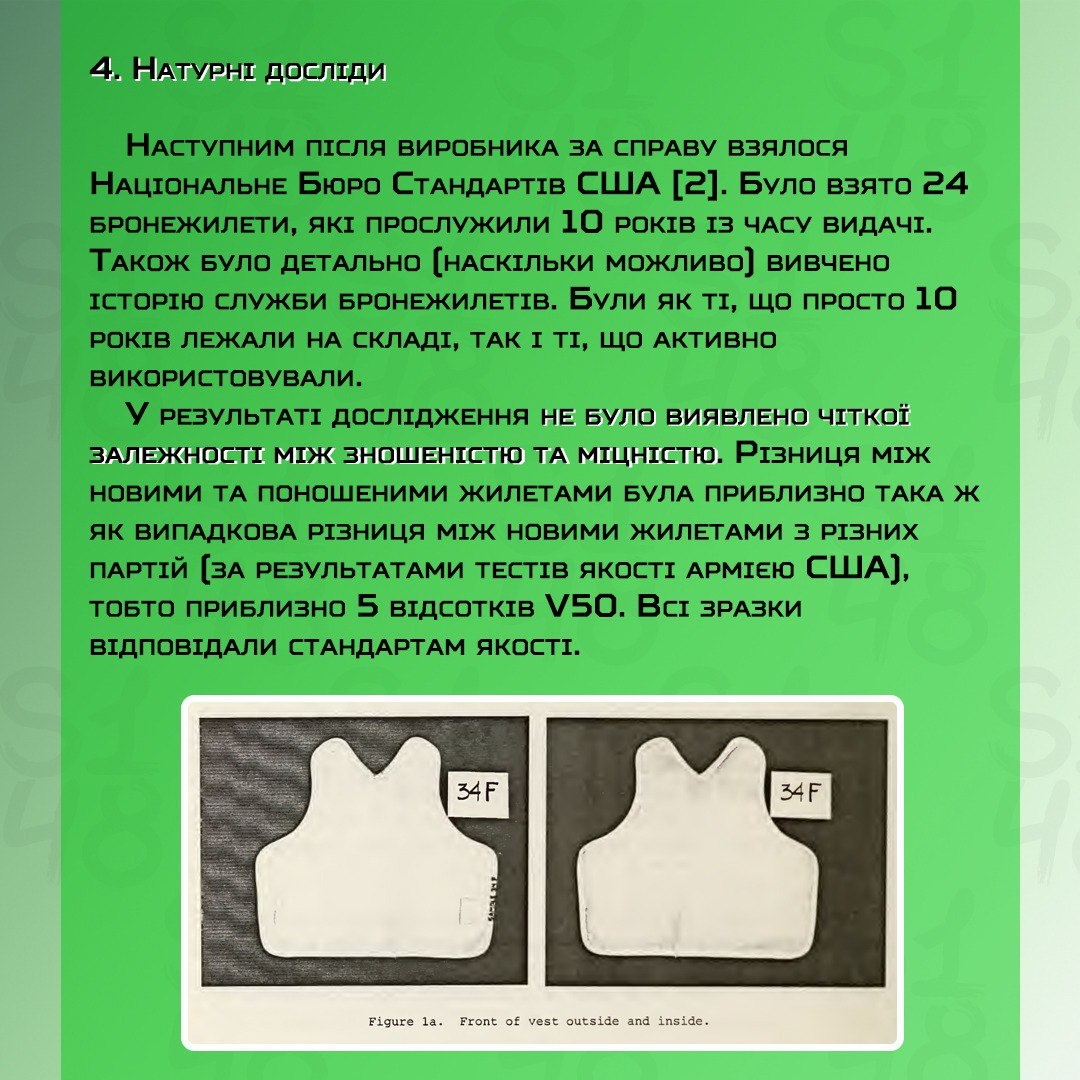
Було виявлене незначне (без виходу за величини стандартів якості) зменшення міцності при намоканні. З цікавого, 2 жилети, що показали себе найгірше, після просушування проявили себе так само як інші. Було виявлено, що у них був пошкоджений чохол, тобто погіршений захист від вологи.
Спеціалісти бюро прийшли до висновку: при стандартних складських умовах вироби з кевлару можуть зберігати свої якості невизначено довго.
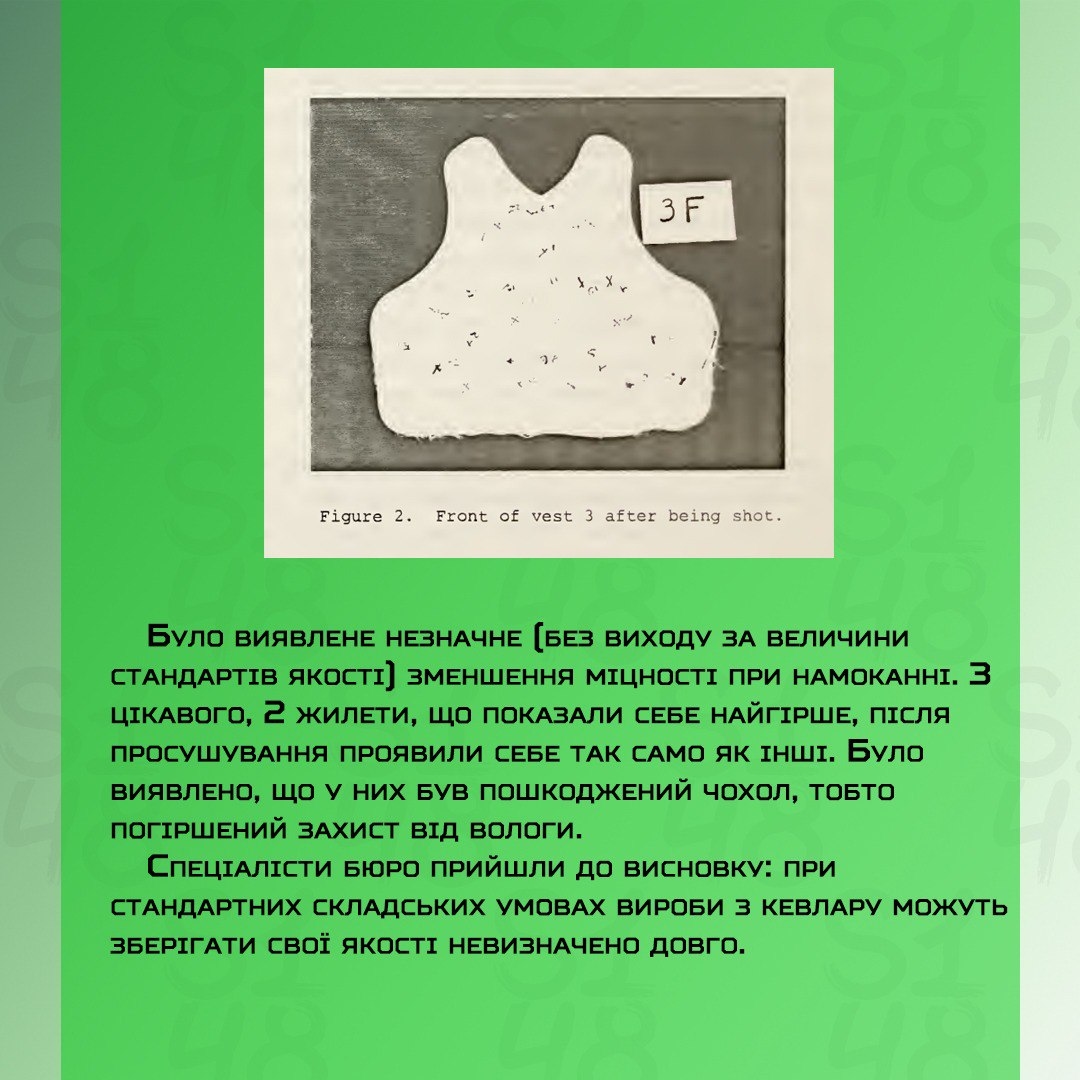
5. Сучасні дослідження
У ґрунтовній праці [3] було розроблено сучасний цикл тестування броні. Використали модифіковану ідею DuPont. За законами перебігу хімічних реакцій, реакції пришвидшуються вдвічі при збільшенні температури на 10 градусів. Тому зношення у 10 років було зменшено до тесту у десять днів за наступних умов: добові перепади температури від 10 до 70 градусів, висока вологість, та, найважливіше, високочастотне згинання.
За висновком роботи, кевлар, що піддавася впливу всіх трьох факторів впродовж 10 днів, зберіг 80 відсотків своєї міцності на розтяг. У випадку, коли були застосовані тільки температура і вологість, зразки зберегли до 88 відсотків міцності, а при тільки згинанні – майже 100.
Робота [4] досліджувала зміну зразків кевлару впродовж 1 року при постійному перебуванні при температурах від 40 до 70 градусів та вологостях від 0 до 73%.
Зразки зберегли приблизно 87% своєї міцності, тобто зберегли захисні властивості. Дані були визнані недостатніми для того, щоб робити висновки про час повної деградації кевлару.
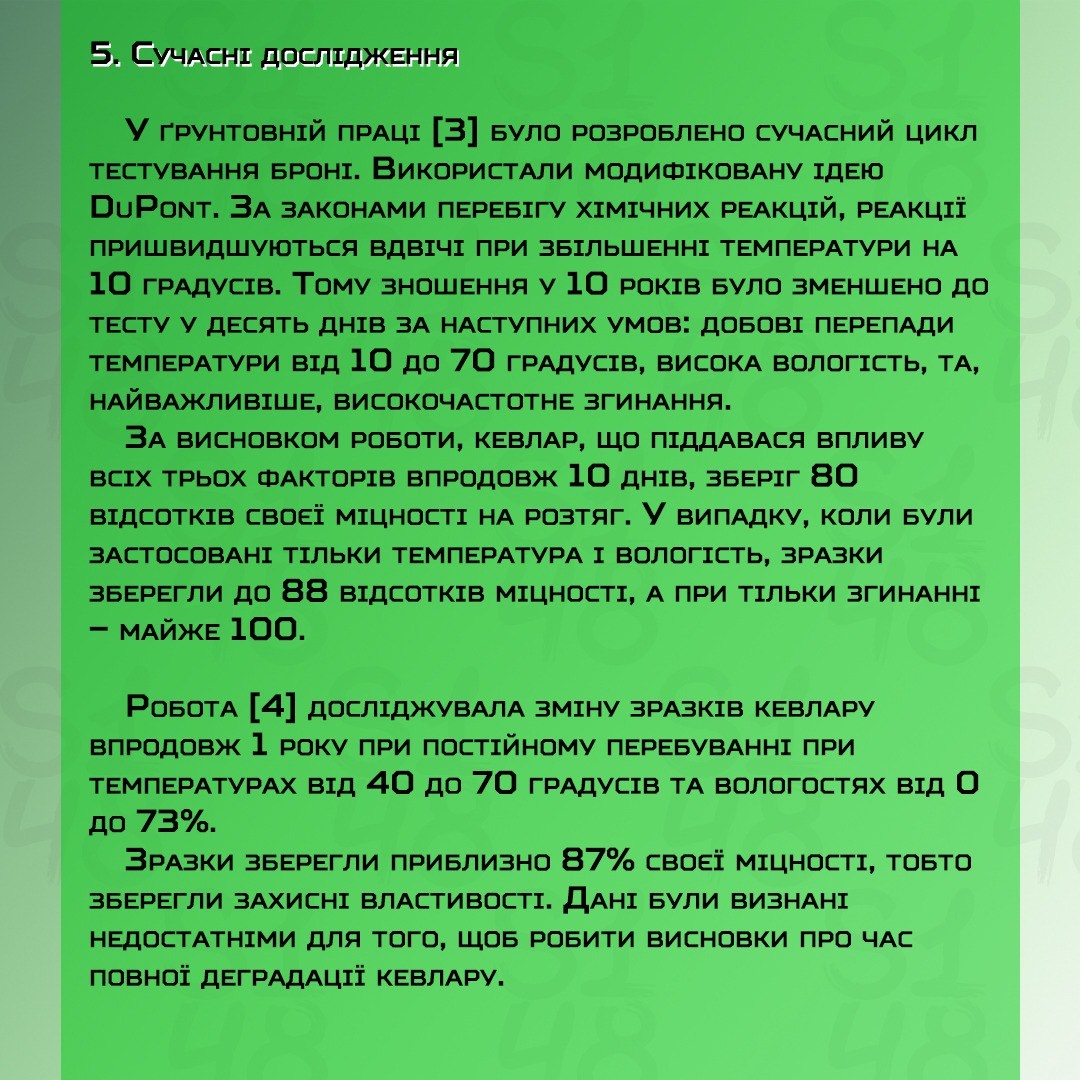
6. Висновки
У роботах 3 і 4 зазначено, що звичайних чохол повністю захищає від дії світла.
В умовах нагріву та вологості хімічного руйнування зразків не відбулось, зміни стосувались тільки волокон тканини.
І тільки при екстремальних умовах роботи (нагрів, вологість, сильний механічний стрес), що відповідають активній експлуатації броні 10 років поспіль, наступає певна деструкція, після якої захисні властивості броні наближаються до властивостей плит, що підвели своїх власників.
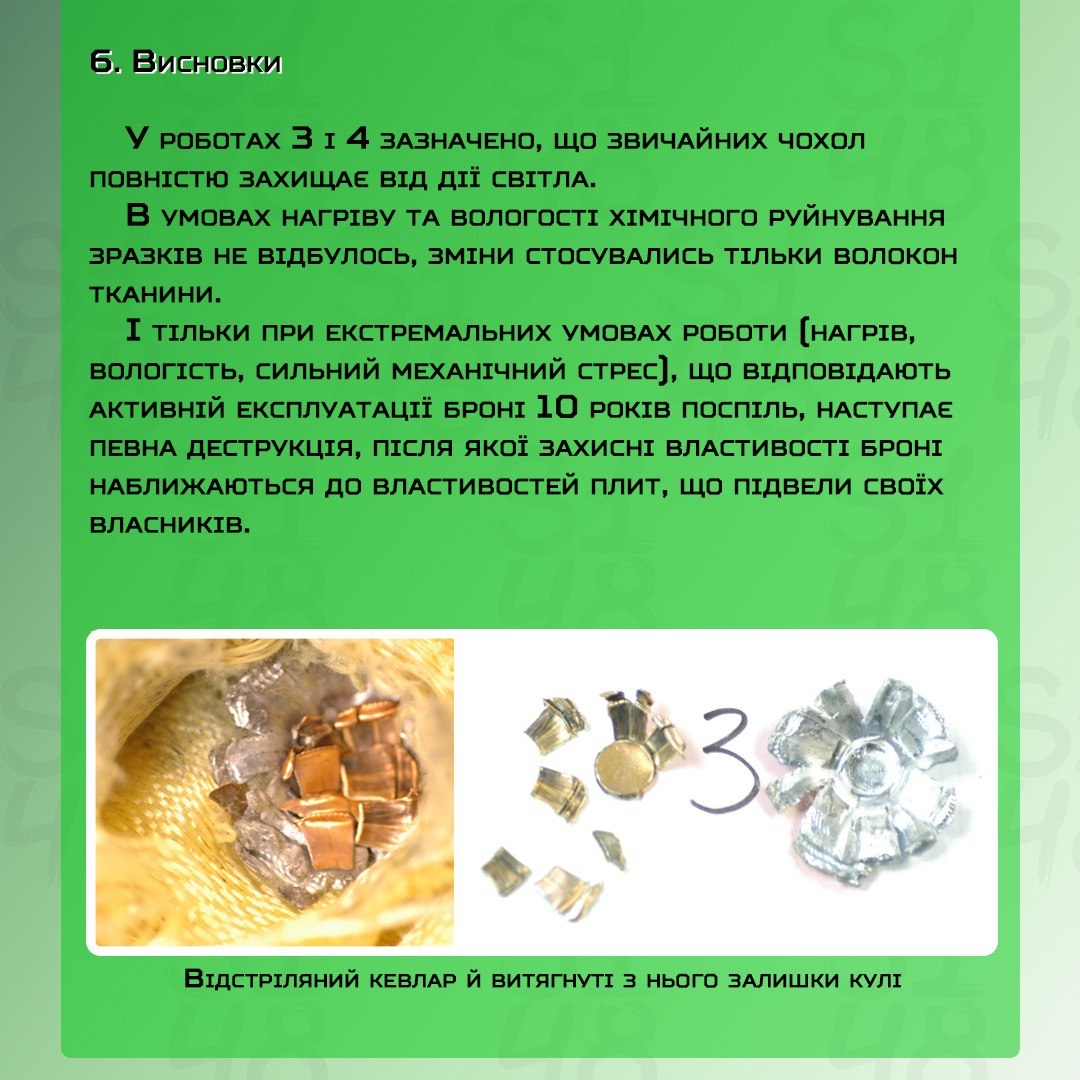
Також, можна сміливо використовувати броню, що поза строком придатності, якщо візуально вона не дуже б.у.
За наявності іржі на шоломах, рваних чохлів та тріщин дуже раджу від носіння утриматись. Якщо ви свою трохи пошкодили, цілком можна зафарбувати шолом та заклеїти герметиком чохол.
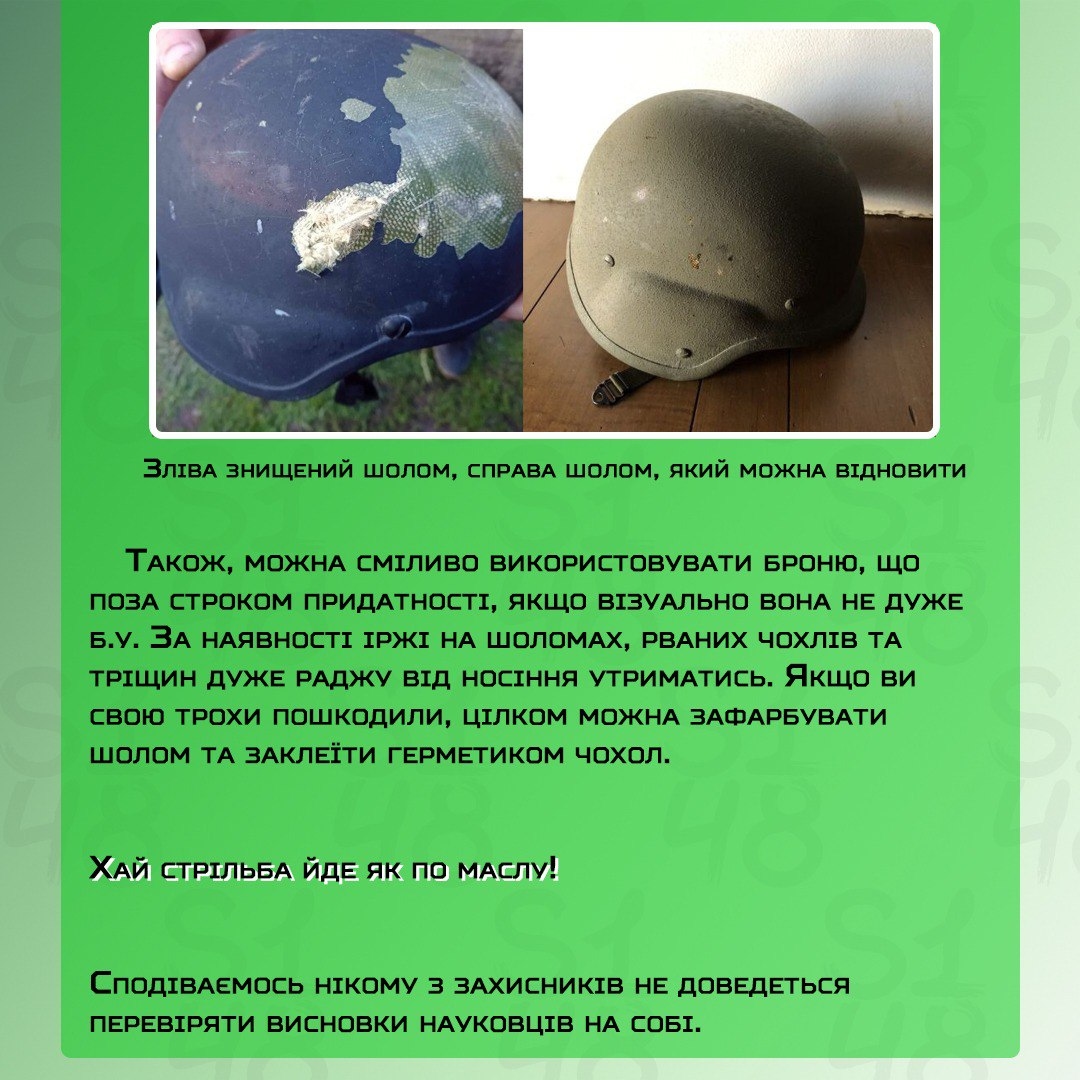
Джерела:
[1]: DuPont Kevlar Survivor’s Club: Rational Replacement Policy – A Recommendation to the Law Enforcement Community. Congress of the United States Office of Technology Assessment 1985; 294: 1302–1310
[2]: Daniel E. Frank, Ballistic Tests of Used Soft Body Armor
[3]: Amanda L. Forster, LONG TERM STABILITY AND IMPLICATIONS FOR PERFORMANCE OF HIGH STRENGTH FIBERS USED IN BODY ARMOR
[4]: A. Engelbrecht-Wiggans, Effects of temperature and humidity on high-strength p-aramid fibers used in body armor
Хай стрільба йде як по маслу!
Наш телеграм: @s148_engineering;
Наш інстаграм: @s148_engineering;
Наш фейсбук: @s148engineering;
Наш ютуб: @S148Engineering;