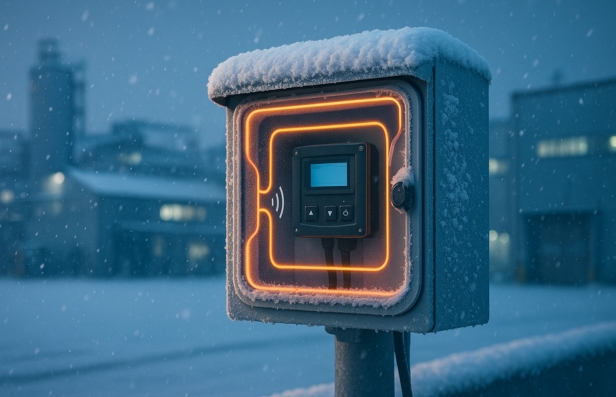
Introduction
Picture a snow-covered factory lot in Minnesota, 6 a.m., February. A security camera lens is frozen over, the gate sensors are sluggish, and the pipes in the outbuilding feel more like popsicles than plumbing. This is where flexible printed heaters come in. These paper-thin warming devices, when embedded into control panels, pipes, or enclosures, can keep critical infrastructure running even when the weather says otherwise.
Forget heated jackets or smart bandages for now. In this blog, we focus entirely on industrial use cases for printed heaters. You’ll learn the technical design rules engineers follow to make sure these heaters operate safely, efficiently, and durably. We’ll cover power requirements, material selection, heater layout, and safety testing. Ready to keep your tech toasty? Let’s get into it.
What Are Flexible Printed Heaters?
Flexible printed heaters are ultra-thin, custom-shaped heating elements made by screen-printing conductive and resistive inks onto flexible substrates like PET, Kapton, or TPU. They generate heat when electric current flows through the resistive ink, while the conductive ink routes power across the heater.
In industrial settings, these heaters are commonly embedded in:
Security camera enclosures to prevent lens fogging or freezing
Water pipes and valves to prevent bursting in cold temperatures
Outdoor control panels or cabinets for thermal regulation
HVAC sensor housings to maintain accuracy in winter
These heaters are typically 0.1 to 0.3 mm thick and shaped to match the equipment they’re warming. Instead of bulky heating coils or mats, think of a flat, printed circuit that delivers heat evenly across a surface.
Define the Application Requirements
Every effective heater starts with a specific industrial use case.
Key considerations:
Flex vs. Rigid: For curved panels or enclosure doors, PET or Kapton are often suitable. TPU may be overkill unless flexibility is crucial.
Environment: Will it face rain, sleet, or power washing? Many heaters are coated with encapsulation layers to protect against water ingress and abrasion.
Form Factor: Sketch out the space. A 6×6 inch camera cover might need a 5×5 inch heating zone, leaving room for connectors and mounting.
Temperature Target: Industrial systems often aim for 40°F to 60°F inside enclosures. Going too warm can damage electronics or overheat sensors.
A common pitfall is not accounting for mounting surfaces. If you're applying a heater to metal, expect better heat transfer, but plan for insulation to keep it efficient.
Calculate Power and Heat Output
Let’s do some math, industrial-style. Suppose you want to keep an outdoor control cabinet at 50°F when ambient temperatures drop to 0°F. You estimate needing 10 watts over a 100 in² surface.
Use the formula:
Power = Voltage² / Resistance
If your power source is 12 volts:
Resistance = 12² / 10 = 14.4 ohms
Keep watt density around 0.1 to 0.2 W/in² for enclosures and up to 1.0 W/in² for frost protection on pipes. If you're not sure, err on the lower side. Overheating is a bigger enemy than underheating in static installations.
Visual analogy time: Voltage is like water pressure, resistance is pipe diameter, and current is flow rate. A narrower pipe (higher resistance) creates more friction (heat), but too much friction (low resistance) can blow the circuit. Know your plumbing.
Optimize Heater Pattern and Size
This is not finger painting. The layout directly affects resistance and thermal consistency.
Best practices:
Use serpentine or zigzag patterns for uniform heat
Keep trace width and spacing consistent
Avoid sharp 90-degree turns that could crack the ink
Add clearance zones for connectors and mounting hardware testing
The goal is to prevent hot and cold spots. A heater that warms unevenly may pass testing but fail in the field. NASA suggests a minimum of 0.010 inch trace width and spacing for durability. That’s a good baseline, even if your heater isn’t going to orbit.
Choose Suitable Materials and Layers
Industrial environments are not forgiving. Materials need to be chosen accordingly.
Substrates:
PET: Budget-friendly, good for flat surfaces
Kapton: Excellent heat resistance, stable performance
TPU: Use only if flexibility is critical
Inks:
Silver: Highly conductive, ideal for bus bars
Carbon: Used for the resistive heating element
PTC (Positive Temperature Coefficient): Self-regulating, safer for enclosed spaces
Encapsulation:
Protective coatings are often essential. Polyurethane or acrylic overlays can guard against moisture, dust, and abrasion. Skip this, and your heater might short out faster than a coffee maker in a thunderstorm.
Plan Connections and Power Supply Integration
A heater is only as good as its power delivery.
Connection options:
Crimped eyelets for metal panels
Flat Flex Cables for board-level integration
Soldered leads for direct wiring
Terminal blocks for easy field installation
Pro tip: Avoid placing connectors near hinges, screw points, or other stress areas. Use strain relief methods like tape overlap, epoxy seals, or rivets.
Power planning is also critical. A 12V, 10W heater draws 0.83 amps. Battery-operated systems may require smart control logic or thermostats. For grid-connected units, integrate with existing PLC or BMS systems.
Test Prototypes and Ensure Safety
Industrial testing is not optional. It’s mandatory.
Checklist:
Use thermal cameras to verify even heating
Cycle-test the heater over 1,000 bends if it flexes
Water and dust resistance testing to IP standards
Electrical safety under fault conditions
You might also consider integrating external thermal cutoffs or inline fuses. PTC heaters can shut themselves down when overheating, which is a strong safety feature in remote or hard-to-reach installations.
Look into relevant standards like UL 499 (electric heating appliances) or IEC 60079 (for hazardous locations). Following standards isn’t glamorous, but not following them can be.
Learn why flexible heaters outperform wired heaters in industrial use - Why are Flexible Printed Heaters Better Than Wired Heaters?
Conclusion
Embedding flexible heaters into printed electronics for industrial use is both an art and a science. It requires a clear understanding of the environment, power constraints, material science, and real-world durability. When done right, these heaters can quietly and reliably protect your most critical systems from the brutal cold.
Think of them as the unsung heroes of industrial reliability. They won’t make headlines, but they’ll keep your cameras watching, your water flowing, and your systems online even when Mother Nature does her worst.
Want more examples or help with your specific use case? Reach out or browse through real-world applications on the Butler Technologies website. The cold never stood a chance.